Plastic extrusion specialists delivering exactness and quality
Plastic extrusion specialists delivering exactness and quality
Blog Article
A Comprehensive Guide to the Process and Advantages of Plastic Extrusion
In the large world of manufacturing, plastic extrusion arises as a very efficient and necessary procedure. Translating raw plastic into constant profiles, it provides to a variety of sectors with its remarkable adaptability. This overview intends to clarify the complex steps involved in this technique, the kinds of plastic apt for extrusion, and the game-changing advantages it brings to the industry. The following discussion guarantees to unfold the real-world impacts of this transformative process.
Recognizing the Fundamentals of Plastic Extrusion
While it might appear complex in the beginning look, the procedure of plastic extrusion is essentially basic - plastic extrusion. It is a high-volume production technique in which raw plastic is melted and shaped into a constant profile. The process begins with the feeding of plastic product, in the type of pellets, powders, or granules, right into a warmed barrel. The plastic is after that melted making use of a mix of warm and shear, used by a turning screw. Once the molten plastic reaches completion of the barrel, it is forced through a tiny opening known as a die, forming it into a preferred form. The designed plastic is after that cooled down, strengthened, and reduced into preferred lengths, finishing the procedure.
The Technical Process of Plastic Extrusion Explained
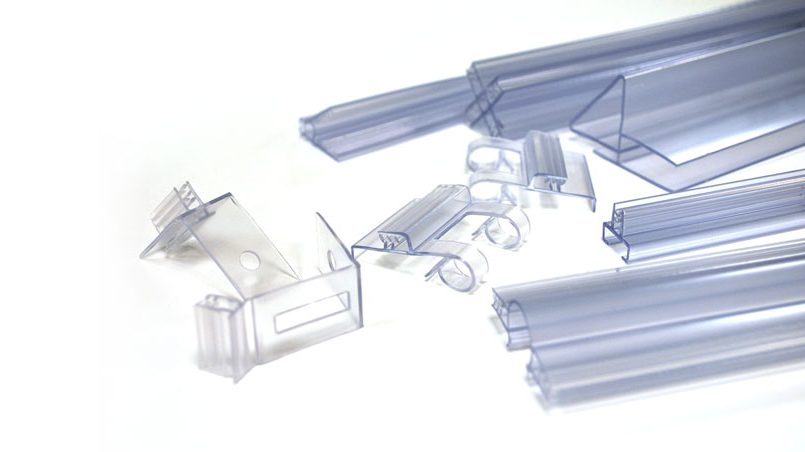
Types of Plastic Suitable for Extrusion
The selection of the right kind of plastic is a critical element of the extrusion process. Numerous plastics provide one-of-a-kind properties, making them extra fit to specific applications. Understanding these plastic kinds can significantly improve the extrusion process.
Contrasting Plastic Extrusion to Various Other Plastic Forming Techniques
Recognizing the kinds of plastic appropriate for extrusion paves the way for a more comprehensive discussion on just how plastic extrusion piles up against various other plastic creating approaches. Plastic extrusion is exceptional when it comes to developing continuous profiles, such as seals, gaskets, and pipelines. It additionally permits for a consistent cross-section along the length of the item.
Trick Benefits of Plastic Extrusion in Manufacturing
In the realm of manufacturing, plastic extrusion provides several significant benefits. One significant advantage is the cost-effectiveness of the process, that makes it an economically appealing manufacturing approach. Furthermore, this strategy offers superior item adaptability and enhanced manufacturing rate, consequently raising general production efficiency.
Economical Production Method
Plastic extrusion jumps to the leading edge as an economical production method in production. This procedure attracts attention for its ability to generate high volumes of material swiftly and effectively, providing makers with considerable financial savings. The main price benefit is the capability to utilize more economical raw products. Extrusion makes use of polycarbonate materials, which are much less pricey compared to steels or ceramics. Even more, the extrusion process itself is reasonably simple, decreasing labor prices. In addition, plastic extrusion needs less energy than typical manufacturing methods, adding to reduced functional prices. The procedure additionally reduces waste, as any kind of excess or defective products can be recycled and reused, offering another layer of cost-effectiveness. Overall, the economic benefits make plastic extrusion a very eye-catching alternative in the manufacturing market.
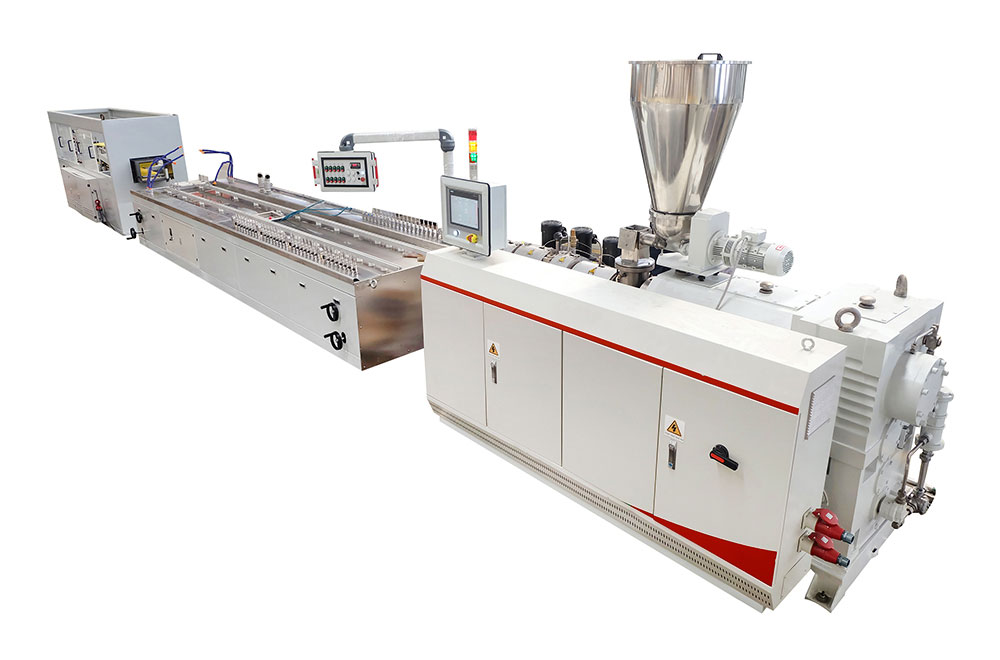
Superior Product Adaptability
Beyond the click now cost-effectiveness of plastic extrusion, another significant benefit in manufacturing depend on its premium product flexibility. This procedure enables the production of a vast range of products with varying styles, sizes, and shapes, from easy plastic sheets to elaborate accounts. The flexibility is attributed to the extrusion pass away, which can be customized to generate the preferred item design. This makes plastic extrusion a perfect solution for industries that call for tailored plastic elements, such as auto, building and construction, and product packaging. The ability to create diverse products is not just valuable in learn the facts here now meeting details market needs however also in making it possible for suppliers to check out brand-new line of product with minimal capital expense. In significance, plastic extrusion's item flexibility promotes technology while boosting operational efficiency. see it here
Boosted Production Rate
A significant benefit of plastic extrusion exists in its boosted manufacturing rate. Few various other production processes can match the rate of plastic extrusion. In addition, the capability to maintain constant high-speed manufacturing without sacrificing item quality establishes plastic extrusion apart from other techniques.
Real-world Applications and Influences of Plastic Extrusion
In the world of manufacturing, the method of plastic extrusion holds extensive significance. The financial benefit of plastic extrusion, mostly its high-volume and cost-effective outcome, has transformed manufacturing. The market is constantly striving for technologies in eco-friendly and recyclable materials, suggesting a future where the advantages of plastic extrusion can be retained without compromising environmental sustainability.
Conclusion
To conclude, plastic extrusion is a highly efficient and effective technique of changing basic materials right into varied products. It provides various benefits over various other plastic developing approaches, including cost-effectiveness, high output, very little waste, and layout flexibility. Its impact is greatly really felt in numerous sectors such as building and construction, vehicle, and consumer products, making it a crucial procedure in today's manufacturing landscape.
Delving much deeper right into the technical process of plastic extrusion, it starts with the choice of the ideal plastic product. Once cooled down, the plastic is reduced right into the required sizes or wound onto reels if the product is a plastic movie or sheet - plastic extrusion. Contrasting Plastic Extrusion to Other Plastic Forming Approaches
Comprehending the types of plastic ideal for extrusion leads the way for a more comprehensive conversation on exactly how plastic extrusion stacks up versus other plastic creating approaches. Few various other manufacturing processes can match the rate of plastic extrusion.
Report this page